A Biased View of Volution Bearing
Table of ContentsAn Unbiased View of Volution BearingThe 6-Second Trick For Volution BearingEverything about Volution BearingVolution Bearing Things To Know Before You Get This
This is the amount of time that a team of apparently identical bearings will certainly complete or exceed prior to the development of a tiredness spall.This calculation can be rather complicated as it depends upon the relative sizes of the radial and thrust lots per various other and the contact angle created by the bearing. It would be also difficult to show all the approaches of computing P for all the bearing types revealed. For tapered roller bearings, the "K" thrust element is used.
Radial cylindrical roller bearings that have opposing flanges on their inner and external races have a minimal capability of taking a drive lots though the size of the rollers. It is so limited that we do not advise users deliberately do this. Appropriate drive loading is using roller ends and flanges for recurring thrust and locating purposes.
Numerous applications do not run at a continuous lots or rate, and to select bearings for a specific ranking life in hours based upon the most awful operating problem could prove wasteful (https://worldcosplay.net/member/1761206). Typically, a duty cycle can be defined for the numerous operating problems (tons and rate) and the percent of time at each
Volution Bearing for Dummies
In such instances, a full responsibility cycle takes place within one transformation of the bearing. Furthermore, the 2 instances can be combined for several expected operating problems with reciprocating activity and different peak loads and speeds. Calculating the score life when tons and speeds vary includes very first computing the L10 ranking life at each operating condition of the obligation cycle.
T1, T2, Tn = percentage of time at different conditions, expressed as a decimal T1 + T2 + Tn = 1 Lp1, Lp2, Lpn = Life in hours for every duration of continuous tons and rate When a bearing does not make a full turning yet oscillates backward and forward in operation, a lower equal radial load can be determined utilizing the formula below: Pe = Po x (/ 90)1/e where: Pe = comparable dynamic radial load Po = real oscillating radial tons = angle of oscillation, in degrees e = 10/3 (Roller Bearings) 3.0(Round Brgs) Some applications generate really high radial and drive tons, and it could not be literally feasible or viable to make use of a solitary bearing that can taking both kinds of lots.
One means to achieve this is to make the fit of the outer races extremely loose in their real estates: generally.5 mm/.020 In. to 1.0 mm/.040 In. Life modification factors permit the initial devices supplier to far better anticipate the actual life span and integrity of bearings that you select and mount in your devices.
Unknown Facts About Volution Bearing
Life change aspects, a1, a2 and a3, can theoretically be better or less than 1. manufacturer.0, depending on their examination. In the OEM's process of anticipating the solution dependability of his/her devices, it is sometimes required to increase the integrity of the chosen bearings to forecast a much longer mean time in between failures
If a reduced worth for L10 is calculated with an a1 aspect, and it is not acceptable, then Get More Information a bearing with greater Dynamic Capability requires to be picked. Dependability - % Ln a1 factor 90 L10 1.00 95 L5 0.64 96L4 0.55 97 L6 0.47 98 L2 0.37 99 L1 0.25 There have actually been several improvements in bearing design and manufacture for many years that have been shown in life tests that cause improved L10 score life.
Lots of bearing applications are much from laboratory problems. It can be hard to justify an a3 element higher than 1.0. Conditions such as high temperature, contamination, outside resonance, and so on will certainly lead to an a3 factor much less than 1. If the lubrication transcends and the running speed high enough, a considerably improved lube film can create in between the bearing's internal call surfaces justifying an a3 aspect better than 1.0.
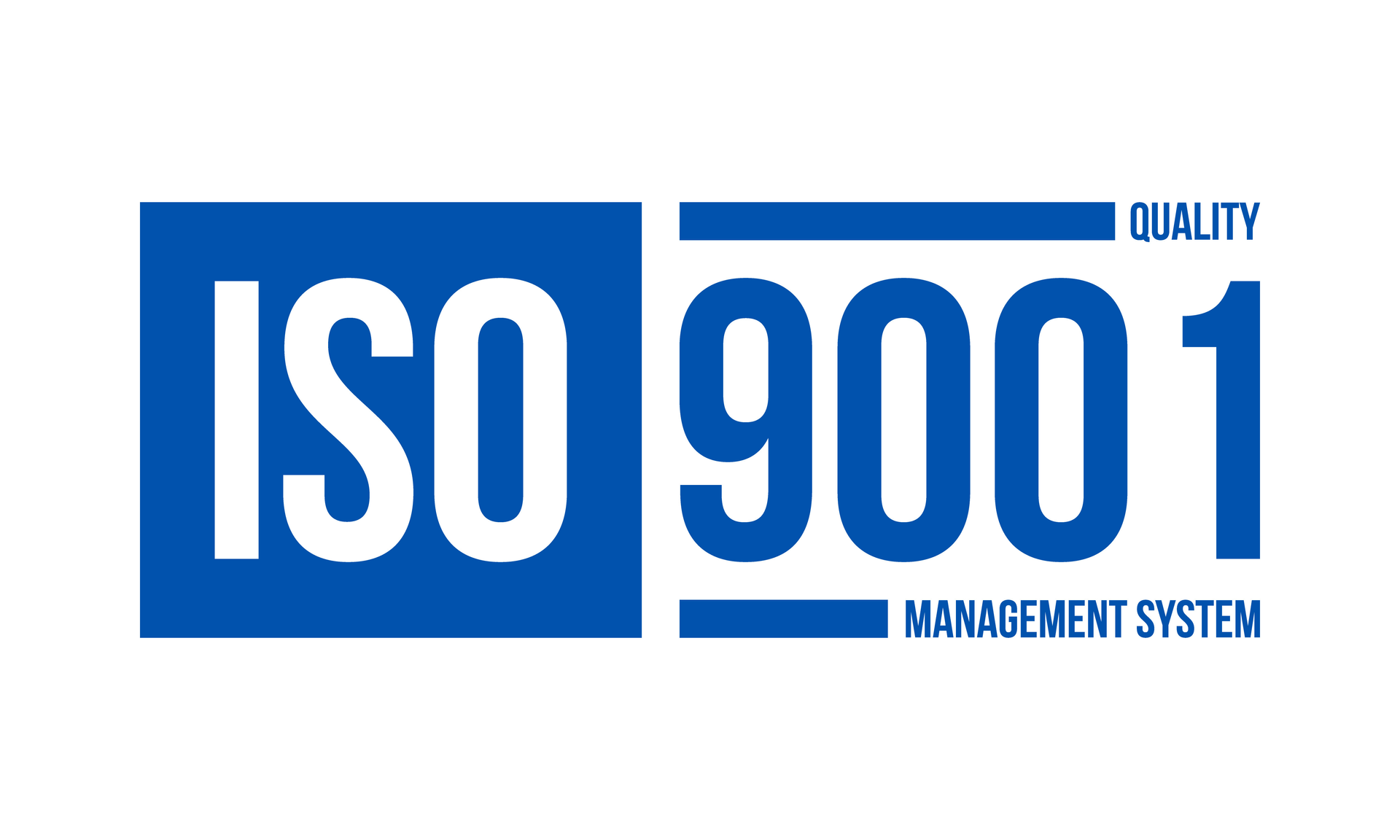
Volution Bearing - The Facts
The following formula is used to determine the System Ranking Life: L10sys = (L1-w + L2-w + Ln-w)-1/ w where L10sys = rating life for the system of bearings L1, L2, Ln = score life for the individual bearings in the system w = 10/9 for round bearings and w = 9/8 for roller bearings It has actually been found out from experience that bearings need a minimal used load to guarantee traction for the rolling aspects so they roll as the shaft begins to rotate. https://volutionbearings.blog.ss-blog.jp/2024-05-06?1715000140.
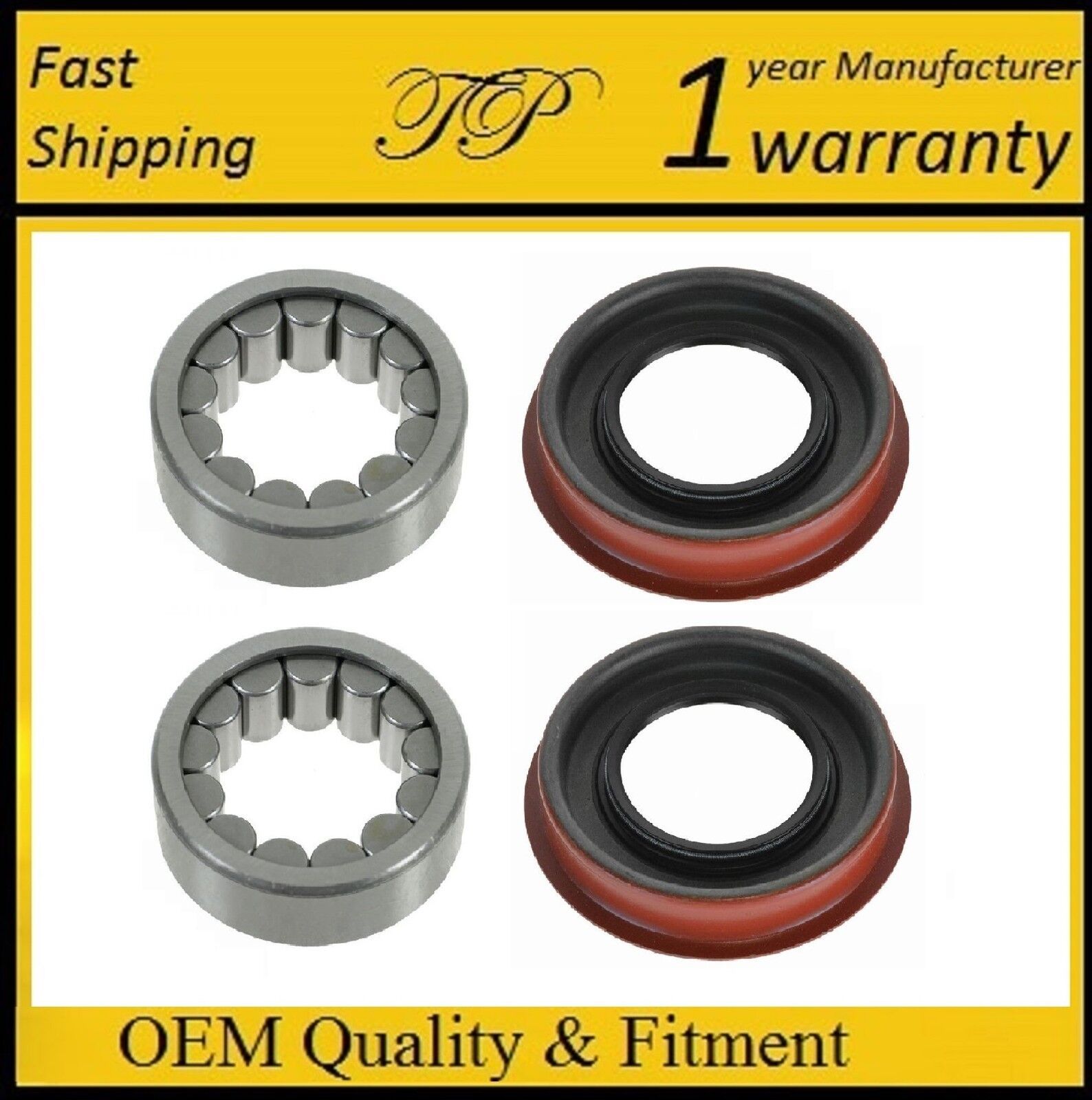
Comments on “Volution Bearing Fundamentals Explained”